Highlight
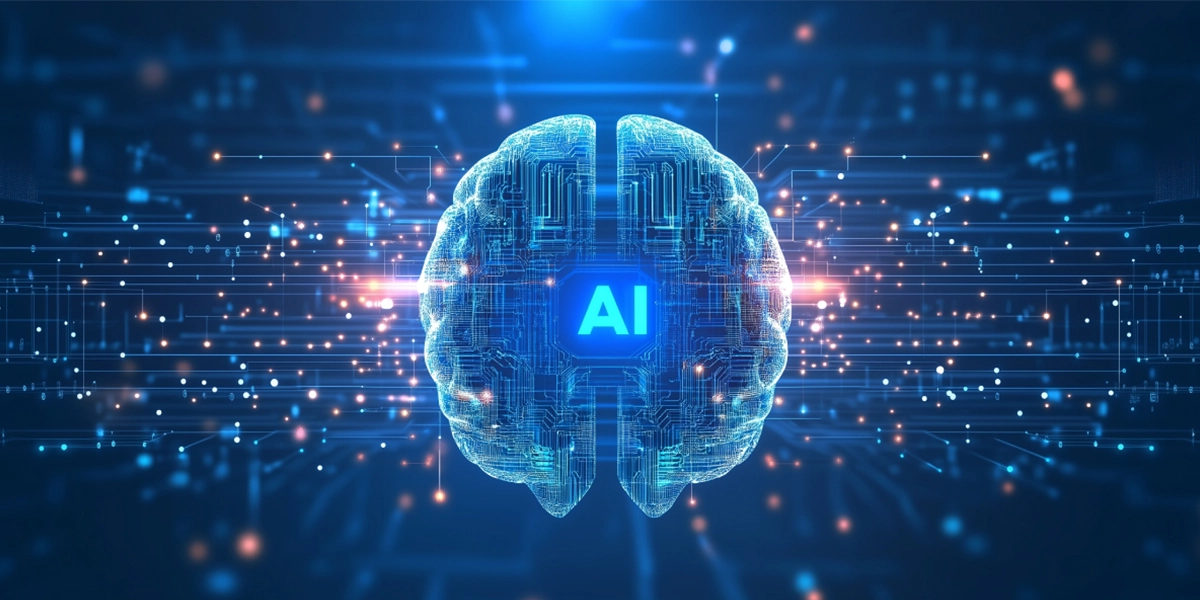
Agentic AI Meets ER&D: Engineering the Next Leap in Autonomy
This is the world of Agentic AI, where intelligent systems that can proactively make decisions, adapt to change, and drive outcomes without human intervention.
Latest Reads
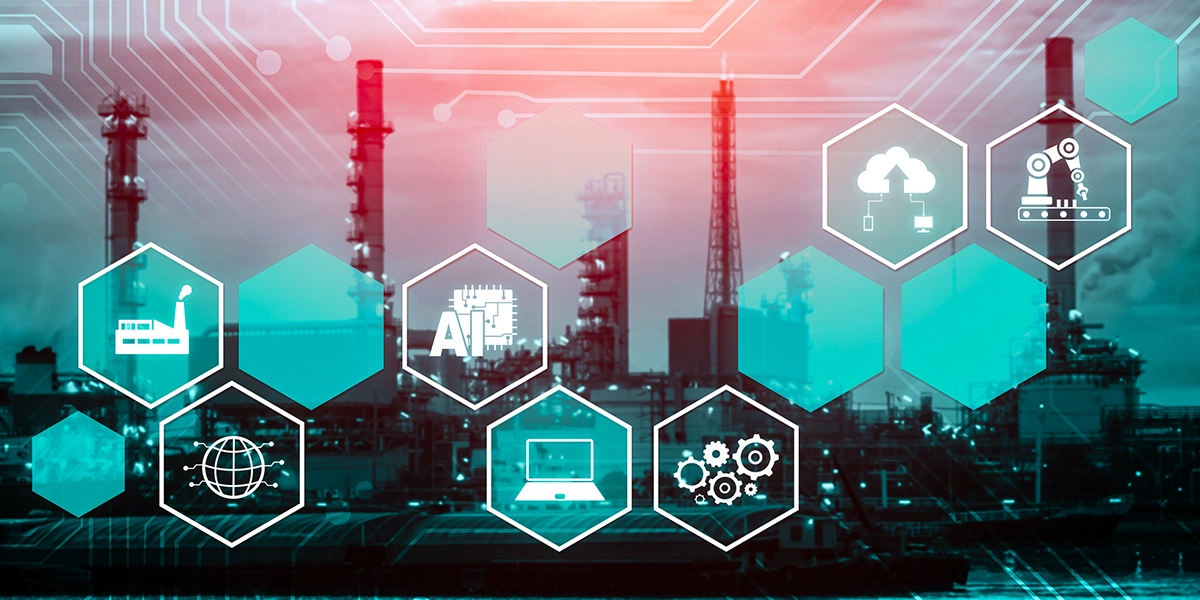
- Plant Engineering
- Artificial Intelligence
Self-Healing Service Desks: Accelerating Digital Experiences
by Ankur Gupta